Advantages of 5-Axis CNC Machining

During the Renaissance period, artists like Michelangelo would use simple tools like a hammer and chisel to complete their masterpieces. That is what they had available to them. Nowadays, that is not the best tools to use in manufacturing. As is the case if you were living in any other time, you’d want the best tools and equipment to bring your ideas to life.
We strongly believe that 5-axis CNC machining, whether you are working with titanium or marble, maybe the best choice for the quickest and highest quality results. If this is your first-time hearing about 5-axis machining or just don’t know if it’s right for your company needs, it’s a good idea to consider some of the benefits of using this kind of equipment and processes.
Before we discuss some of the advantages, let’s clear up what 5-axis refers to.
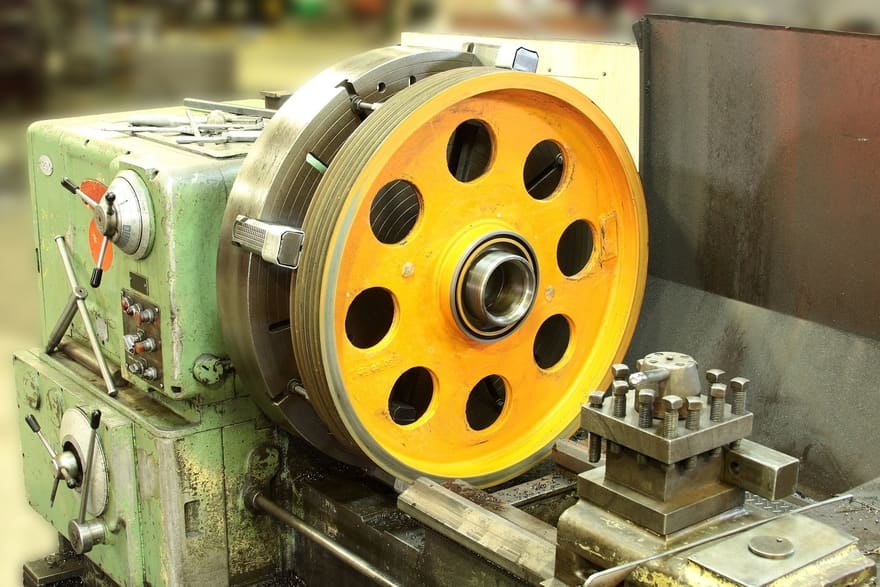
Understanding 5-Axis Machining
5-Axis CNC machining is a form of CNC that moves cutting tools and equipment across five different Axis. As the tool is always moving along each axis, its tip is always set at a perpendicular position to the part. This form of CNC prototyping in China allows you to design and create various intricately cut and shaped components and parts.
Noe that you understand the basics, let’s discuss some of the major benefits of this form of machining.
5-Axis CNC Machining Benefits
There are various benefits you can avail yourself and your business by using 5-axis machining. Below we will look at six.
Avoid Collisions
With 5-axis machining you can avoid collisions occurring between the cutting tool and the tool holder by tilting the cutting tool or table.
Drilling Holes
With a 5-axis setup, you can drill several holes with different compound angles quickly and efficiently. Compared to if you were using a 3-axis machine, where a new setup would be required to drill each hole, it is quite a time-saver being able to do it in one fell swoop.
Improved Lifespan of Tools
With 5-axis machining you can ensure the cutting position is always just right and there is a consistent chip load, two factors that will help increase the lifespan and cycle time of the tool.
Complex and Intricate Components
When you use a 5-axis machining setup you can machine more complicated and intricate components that would, with a 3-axis machine, require a cast being made. This has particular uses for things such as aerospace machining, which requires tight tolerances and precision. If you use prototypes or small runs, you can machine the necessary components in just a few weeks rather than having to wait for the casting to be completed, which can often take a few months.
Smaller and Compact Cutting Tools
With 5-axis machining you don’t need to use excessively long cutting tools, because you can lower the cutting tool head down and maneuver the cutter into position appropriately. Primarily, this helps improve the speed of cutting while reducing the pressure required. It also decreases the amount of vibration generated by the tool, which can create unwanted cores and cavities. As a result, you will achieve smoother finishes.
Single Setup
When you are working with a 3-axis machine, it requires numerous setups which can cause frustrating errors and higher costs. With a 5-axis machine, however, you can machine intricate parts with just one setup, which reduces human error, costs, time spent and increases efficiency and accuracy.
ok, this is a good article.